Loch und Löcher
Die Anforderungen an eine Bohrung können sehr unterschiedlich sein: Es gibt grimmige Zeitgenossen, deren alter W124 schon bei Sprühregen so viel Wasser nimmt, dass der Fußraum der Daimler-Dschunke regelmäßig überflutet ist. Weil der Daimler aber rollt und zumindest die Technik nicht aufgeben will, muss das Wasser raus. Sind die kubikmetergroßen Berge von Reiseabfällen entsorgt, ist diese Entwässerung formschön und elegant mit einigen Bohrungen im Fußraum hinzubekommen: fein!
So ein Fußraumloch lässt sich im Prinzip mit einem Dosenöffner oder einer abgesägten Schrotflinte anbringen, ist mit einer Bohrmaschine jedoch am einfachsten zu machen. Diese Löcher stellen keine hohen Ansprüche an die Qualität. Bessere Bohrungen finden sich an Maschinenteilen. Will man ein ausgerissenes Stehbolzengewinde am Motorblock mit einem Gewindeeinsatz versehen, so hat man für diese Aktion lediglich einen einzigen Versuch, der den Block und womöglich die ganze Kutsche vom Edelschrott trennt.
Genaues Wissen um das wie und was beim Bohren ist hier deswegen unerlässlich. In diesem Teil der Bohren- und Gewindeschneidenserie geht es um das Bohren an sich, die Geschwindigkeiten und wie man größere Löcher bohrt oder kleine Bohrungen größer macht.
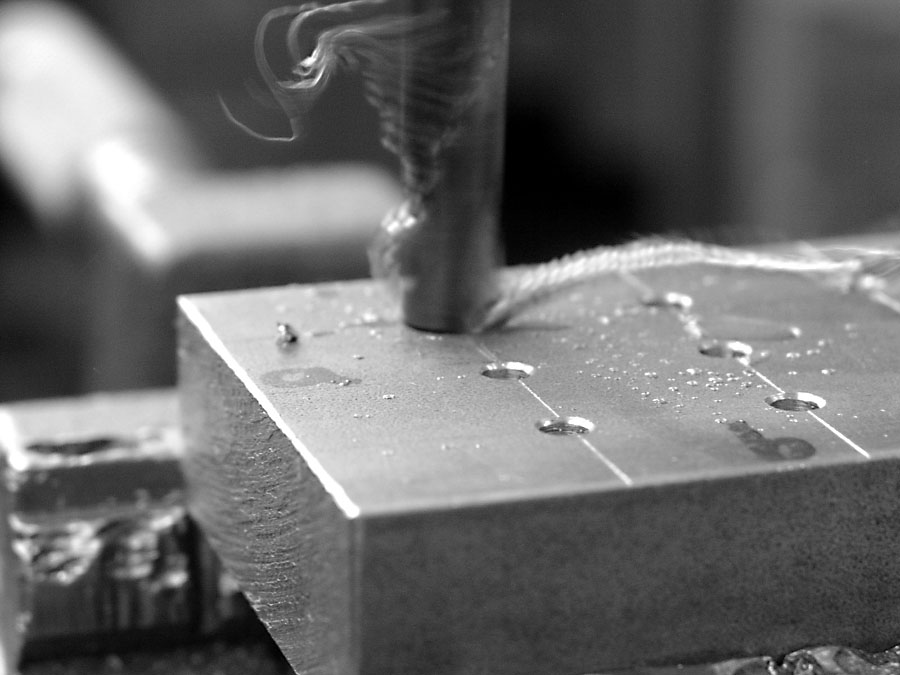
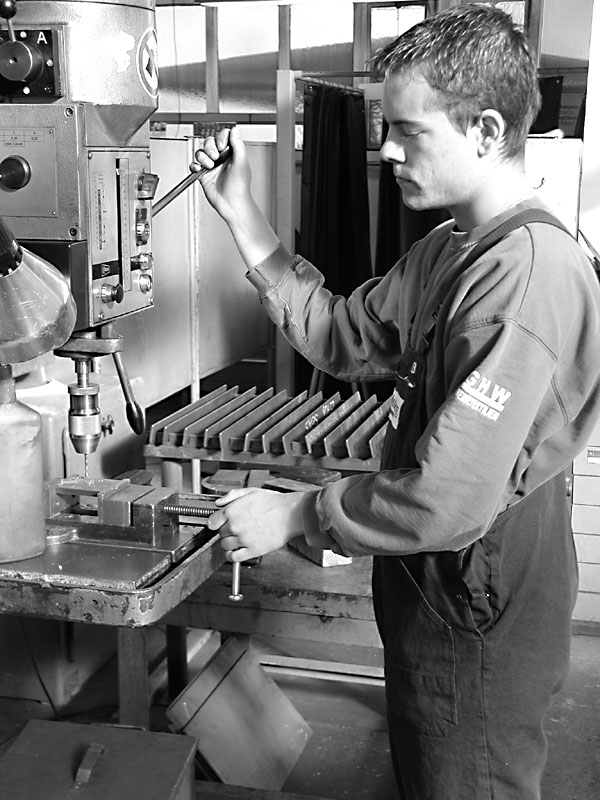
Bohren ins Volle
Wohin mit dem Loch? Wegen dieser simplen Frage steht vor allem Bohren ins Volle der Anriss und ein Körnerpunkt. Mit so einem Punkt versehen, lässt sich der Bohrer bei stehender Maschine wunderbar sauber über der Bohrung in spe positionieren und dann sanft anbohren.
Gängige Spiralbohrer haben bis zum Durchmesser von rund 8 Millimetern die Eigenschaft, ein wenig zu federn und sich zu biegen. Will man also mit einem kleinen Bohrer vorbohren oder gleich ins Volle jagen, sollte dieses Ausweichen mit kalkuliert werden – die Biester biegen sich und bohren möglicherweise nachher ganz woandershin.
Bohrt man ins Volle, so ist natürlich interessant, mit welchem Bohrer, welcher Maschine und vor allem in welchen Werkstoff. Es gibt Kombinationen, die schlicht nicht zu machen sind – der Versuch, mit einem 10mm-Spiralbohrer und einer 700Watt-Handbohrmaschine in rostfreien Edelstahl zu bohren, wird mit hoher Wahrscheinlichkeit scheitern (Es sei denn, der Mann an der Maschine ist Seemann, raucht Pfeife und hört auf den Namen Popeye).
Üblicherweise ist Edelstahl nämlich verflucht hart und zäh und schreit nach hohen Kräften und standfesten Schneiden, um überhaupt in Spänen aufzugehen. In diesem Fall ist natürlich angezeigt, das Werkstück mit einer Säulenbohrmaschine zu bearbeiten.
Die bringt viel höhere Vorschubkräfte zustande und hat in aller Regel auch mehr Drehmoment. Ist das nicht möglich, muss vorgebohrt werden. Dieses Vorbohren beseitigt nicht nur den Kraftverlust durch die lästige Querschneide (voriger Artikel), sondern zerspant natürlich schon einen guten Teil der Materials.
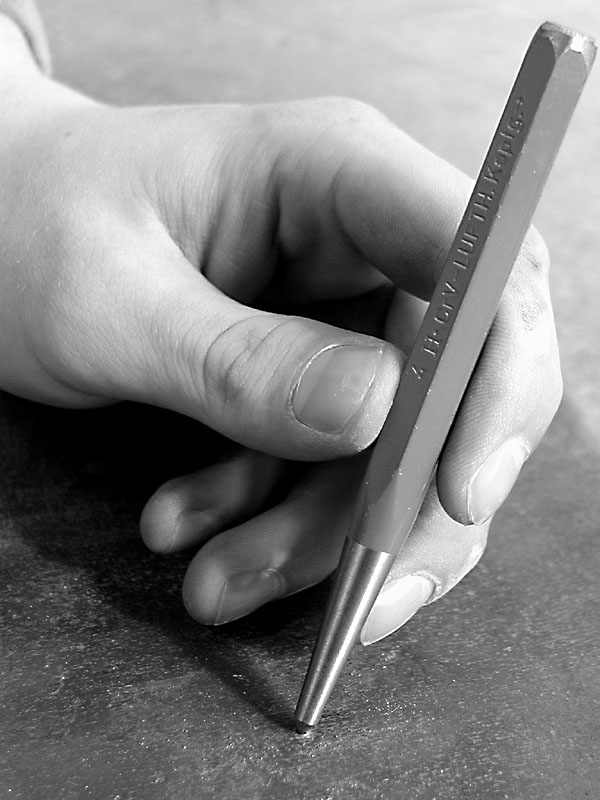
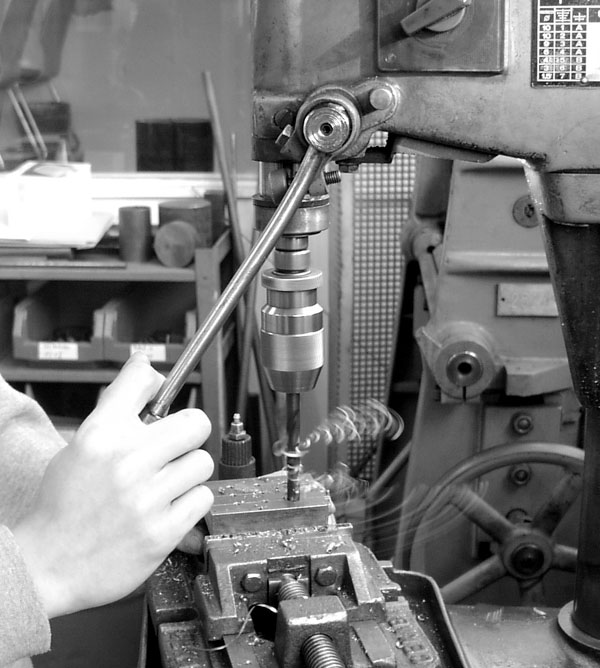
Bohrwasser / Kühlschmierstoff
Wohin verschwindet die ganze wertvolle Kraft und Arbeit, die das Atomkraftwerk von um die Ecke in die Bohrmaschine liefert? Die Antwort ist wie immer simpel: vor allem in Wärme. Nur ein geringerer Teil wird dazu verwendet, Atome oder Moleküle auseinanderzuruppen. Weil das so ist und beim Bohren eine erhebliche Menge Wärme entsteht, muss man bei größeren oder tieferen Bohrungen in jedem Fall kühlen.
Dieses Kühlen hat zuerst natürlich die Aufgabe, das Werkzeug kühl zu halten. Wir hatten das schon: Bohrerspitze beim Schleifen zu heiß geworden, zack, ausgeglüht. Um das zu verhindern, wird gekühlt. Darüber hinaus hat das, was man beim Kühlen an Werkzeugmaschinen verwendet, noch eine andere angenehme Eigenschaft. Das Zeug schmiert und hat damit schon eine zweite Aufgabe: Mit Schmieren und Salben verringert sich nämlich die für das Atome-zerreissen nötige Kraft. Darüber hinaus sorgt das Schmieren für deutlich bessere Oberflächen und Maßhaltigkeit.
An allen Bohrmaschinen, Dreh- oder Fräsbänken sind deshalb kleine Rüssel angebracht, die bei laufender Maschine mittels Pumpe eine gelbliche Lorke auf das Werkstück spritzen und so die Schneide und das Werkstück kühlen.
Diese milchige Suppe hat je nach Schraubergeneration oder Landstrich verschiedene Namen und heißt mal „Bohrwasser“, „Bohrmilch“ oder ganz technisch und korrekt „Kühlschmieremulsion“. Letzterer Begriff trifft es ziemlich genau; das Zeug ist eine Emulsion auf Wasser und Öl. Damit die Plempe emulgiert und nicht im Schrank schimmelt, haut der Hersteller gehörige Mengen Chemie und Fungizide in den Kanister – auch wenn es in der Praxis nicht zu machen ist, sollte man Hautkontakt mit der Kühlschmiersuppe deshalb wo möglich vermeiden.
Festzuhalten bleibt, dass eigentlich jede Bohrung, bei der Wärme entsteht oder bei der es auf eine saubere Oberfläche ankommt, gekühlt werden sollte. Ist kein Bohrwasser zur Hand (dass es eh nur in größeren Gebinden und als Konzentrat gibt), geht auch schnödes Leitungswasser. In diesem Fall kämpft man aber anschließend gegen Gevatter Rost, so man nicht direkt nach dem Bohren alles blitzeblank wischt und trocknet.
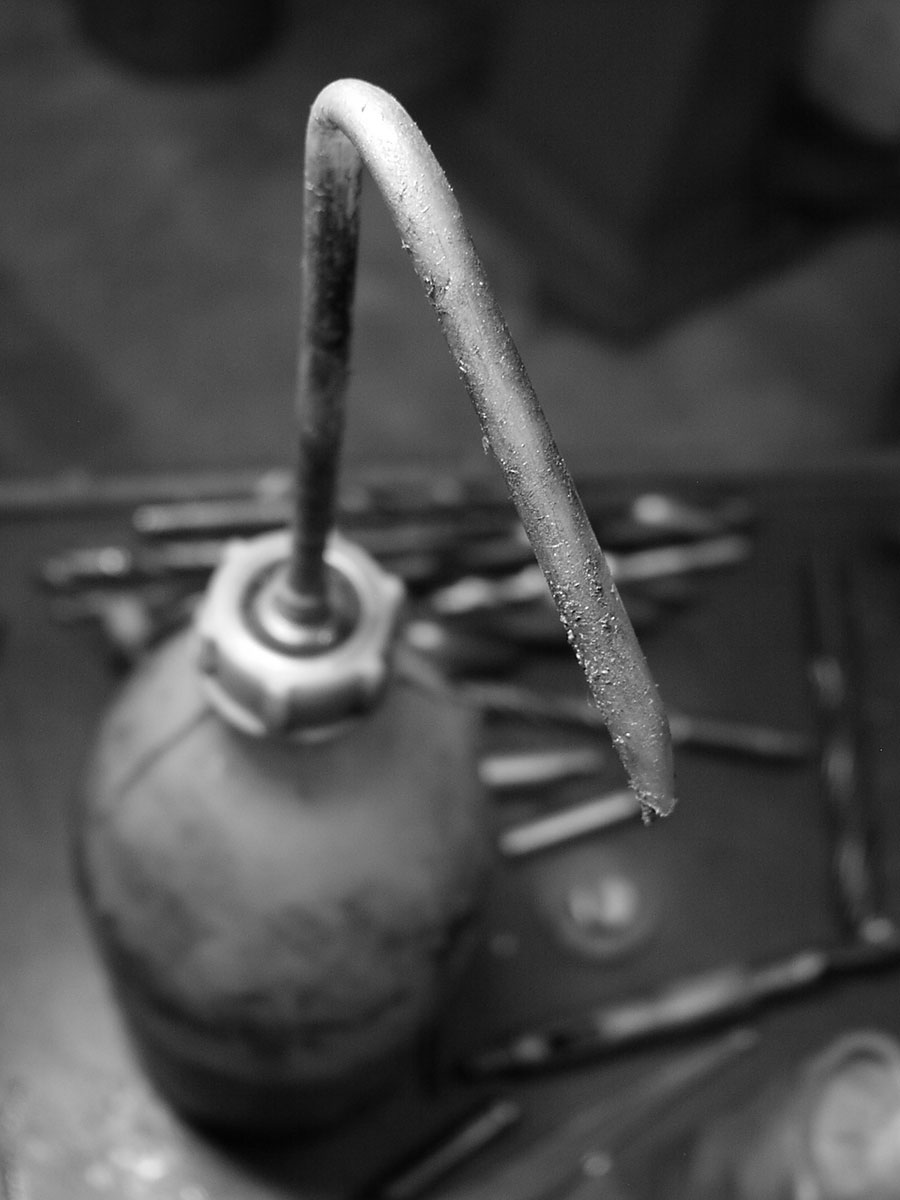
Schnittgeschwindigkeit
Mit der Schnittgeschwindigkeit beim Bohren verhält es sich genauso wie mit der Schnittgeschwindigkeit beim Meißeln. Hier jagt man den Kreuz- oder Flachmeißel schnurgerade ins Metall – wenn das Werkstück lang genug und der Meißel hinreichend schnell wäre, könnte man die Schnittgeschwindigkeit in Kilometern pro Stunde oder Meter pro Sekunde angeben.
Beim Bohren bewegen sich die Schneiden allerdings nicht munter geradeaus, sondern drehen sich im Kreis. Das bedeutet, dass die Schnittgeschwindigkeit am äußeren Ende des Bohrers höher ist als im Zentrum. Auf ein simples Kinderkarussell übertragen, könnte das Balg in der Mitte des Karussells in aller Seelenruhe Gameboy spielen, während den Rangen am Rand des Spielgerätes die Fanta hochkommt – die Geschwindigkeit ist außen größer.
Im Fall unserer Bohrerei bedeutet das die simple Feststellung: mit größerem Bohrer steigt bei konstanter Drehzahl die Schnittgeschwindigkeit (einfach weil die Geschwindigkeit an der äußersten Kante des Bohrers größer ist).
Die Drehzahl hatten wir bisher noch nicht im Rennen – die ist nämlich ein variabler Wert. Geht man davon aus, dass es ein Optimum an Schnittgeschwindigkeit gibt, bei dem der Bohrer nicht sofort verglüht und die Arbeit noch vor Weihnachten fertig wird, so liegen also diese Schnittgeschwindigkeit und der Bohrerdurchmesser fest. Wie kommt man aber zur Drehzahl? Schlaue Leute haben sich ein Förmelchen ausgedacht, mit dem man die Drehzahl passend zur Schnittgeschwindigkeit und dem Bohrerdurchmesser ausrechnen kann.
Die Formel lautet wie nebenstehend. v ist dabei die Schnittgeschwindigkeit, pi ist 3,1415 und d ist der Bohrerdurchmesser in Millimetern. Für die Schnittgeschwindigkeit sollen in diesem Fall solide 20 Meter pro Minute für HSS als Schneidstoff und Baustahl als Werkstoff eingesetzt werden. Bohrerdurchmesser soll 10 Millimeter sein und pi pi. Damit ergibt sich rundherum eine Drehzahl n von rund 636 Umdrehungen pro Minute. Ein toller Wert, der jeden Mathelehrer glücklich macht, aber mit der Praxis nichts zu tun hat.
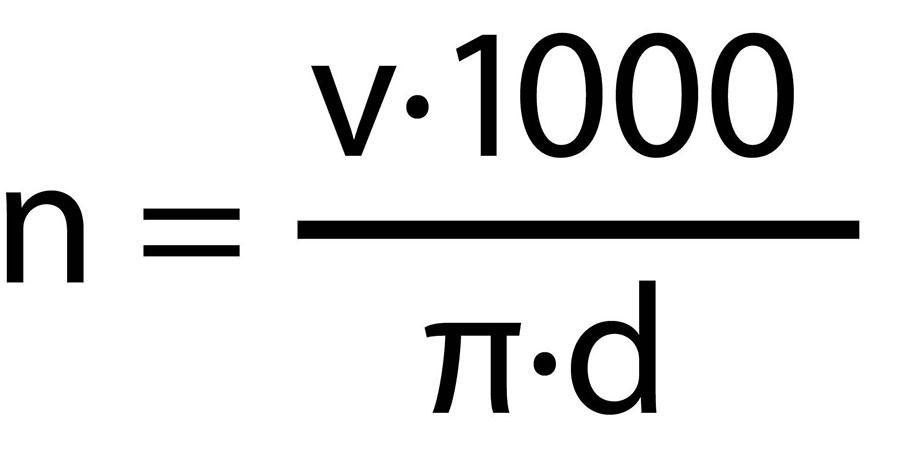
Drehzahl einstellen
Die Berechnung im vorigen Absatz hat eine Drehzahl von 636 Umdrehungen pro Minute ergeben. Das erste Problem beim Übertragen in die Praxis ist, das die Bohrmaschine vermutlich keinen Gang hat, bei dem die Maschine auf 636 Touren läuft. Üble Gemeinheit.
Selbst 640 Touren wird man vergeblich suchen und schon wird offenbar, was es mit dieser Drehzahlrechnerei auf sich hat: sie ist immer nur ein Näherungswert. In der Praxis stellt man die Maschine nämlich stets so ein, dass sich Werkstück, Werkzeug, Maschine und Mann gut fühlen.
Gute Dreher und Fräser hassen diese Formeln oder Drehzahltabellen regelrecht – sie stellen ihre Maschinen immer nach Augenmaß ein und geben acht, wie sich die Zerspanung anhört. Rattert oder quietscht da was, ist die Drehzahl falsch. Beim Bohren ist das genau so; hier sollte man mit der Zeit ein Gefühl entwickeln, welche Drehzahl die richtige ist.
Noch dazu versteht sich diese Drehzahl nur auf die genannten Werkstoffe und die Arbeit mit Kühlmittel. Ungekühlt oder mit Superbohrern oder in anderem Werkstoff sehen die Drehzahlen und die davor stehende Schnittgeschwindigkeit ganz anders aus.
Um also den teuren Spiralbohrer zu schonen oder den ständigen Gang zum Schleifbock zu sparen, muss man einfach weniger Tempo wählen. Weil in der Werkstatt nicht überall ein Taschenrechner zur Hand ist, sind auf vielen Säulenbohrmaschinen Diagramme vorhanden, die für unterschiedliche Schnittgeschwindigkeiten und Bohrerdurchmesser bestimmte Drehzahlen empfehlen – das ist eine gute Hilfe, wenn man überhaupt nicht weiß, was man einstellen soll.
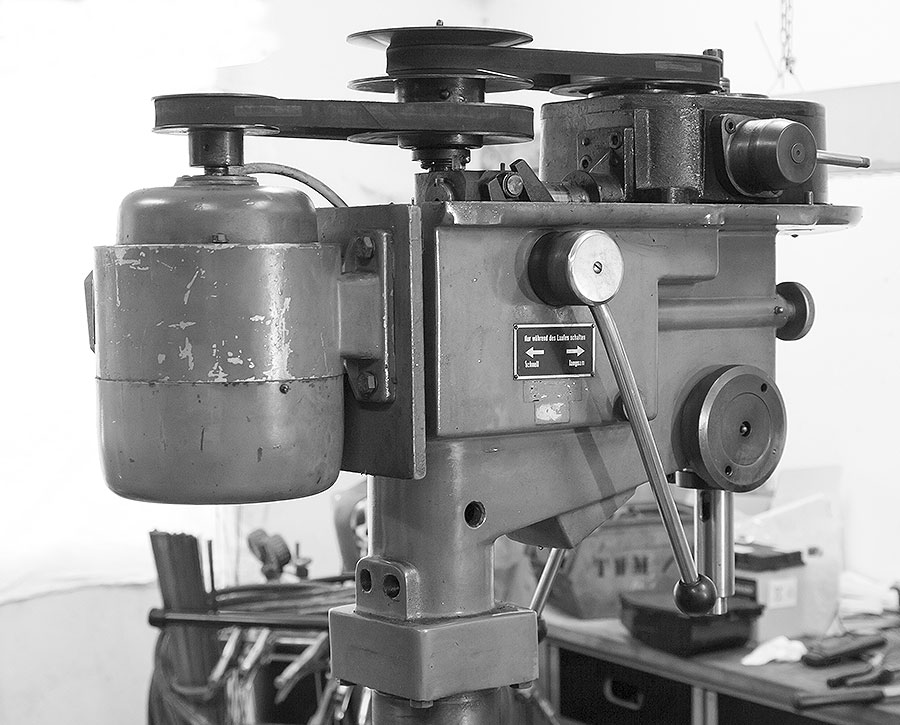
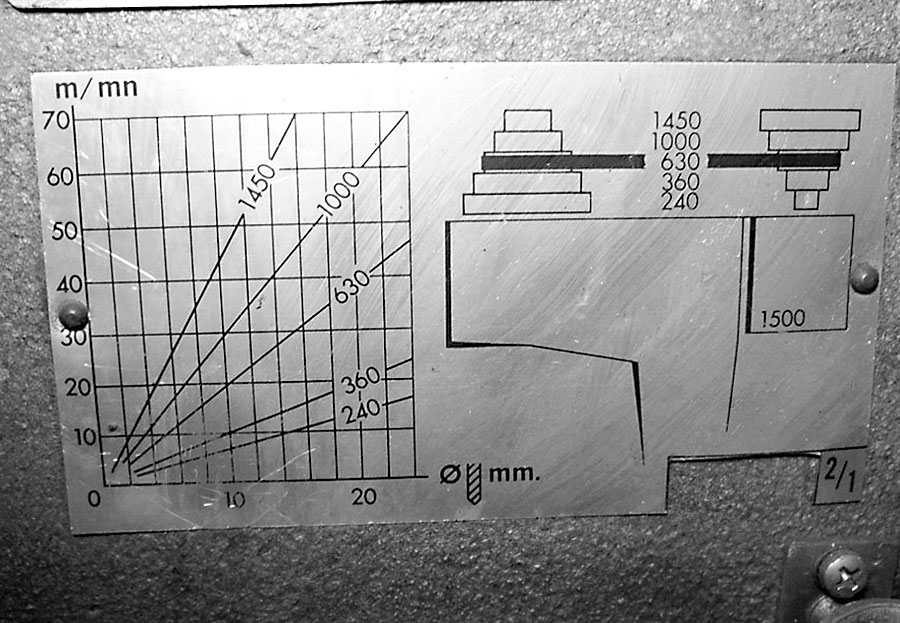
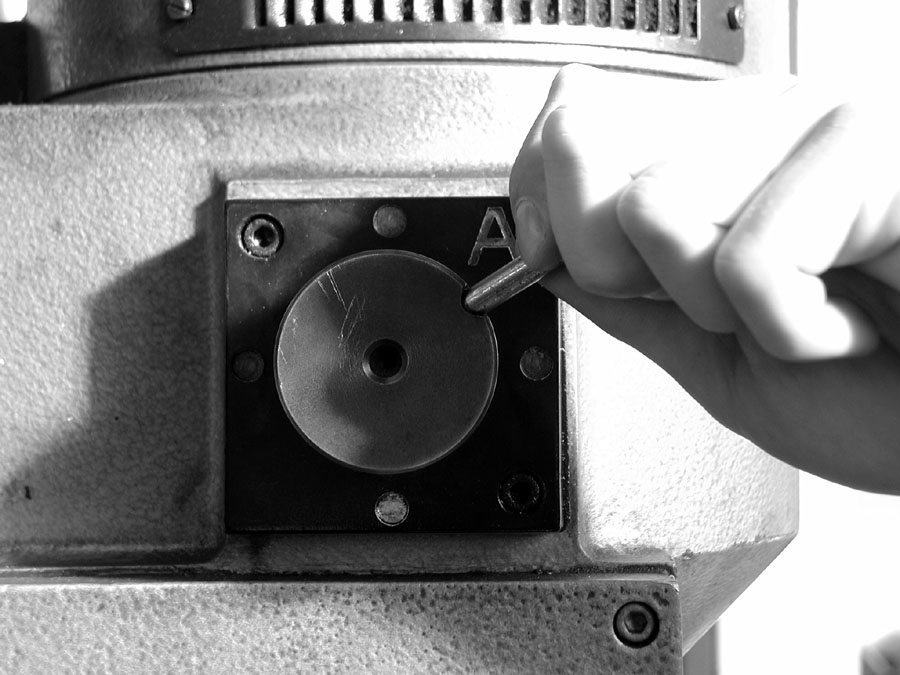
Ins Volle bohren
Die eben genannte Drehzahlrechnerei bezieht sich auf das Bohren ins Volle. Hat man aber schon ein lustig Löchlein produziert, um die Quälerei mit der Querschneide zu ersparen und die Vorschubkraft zu senken, muss die Schnittgeschwindigkeit (und damit auch die Drehzahl) niedriger liegen.
Beim Bohren ins Volle ist nämlich die Hauptschneide, beziehungsweise beide Hauptschneiden, in ihrer ganzen Länge im Eingriff. Die Schnittkraft an der Schneide verteilt sich damit schön gleichmäßig auf die Schneide und lässt sie halbwegs gleich stark verschleißen. Im Gegensatz dazu wird die Schneide beim Aufbohren nur auf einem kleinen Teil belastet. Deshalb muss die Drehzahl niedriger liegen, damit die Schneide an diesem Punkt nicht ausbröselt und übermäßig schnell kaputt geht.
Für normale Aufbohrerei von vielleicht 4 auf 10 Millimeter hat sich bewährt, die Schnittgeschwindigkeit und vor allem den Vorschub einfach zu halbieren. Mit etwas Gefühl sieht man ziemlich schnell, wie viel man dem Bohrer zumuten kann oder nicht. Beim Aufbohren von 8 auf 10 Millimeter ist die Belastung der Hauptschneide nur noch punktuell, zudem ist die Gefahr groß, dass das Ding rattert und schnattert und überhaupt kein sauberes Loch mehr produziert.
In so einem Fall ist es angezeigt, die Drehzahl auf den niedrigsten Wert einzustellen und ordentlich Kühlmittel einzusetzen, damit die äußerste Ecke der Hauptschneide nicht ausfranst und die Bohrung maßhaltig wird.
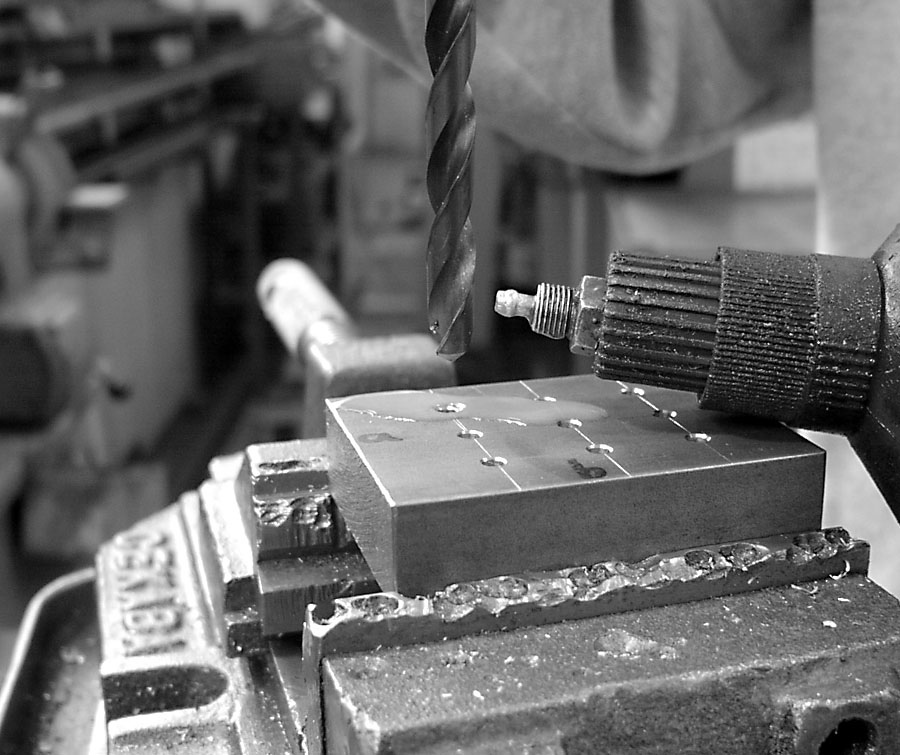
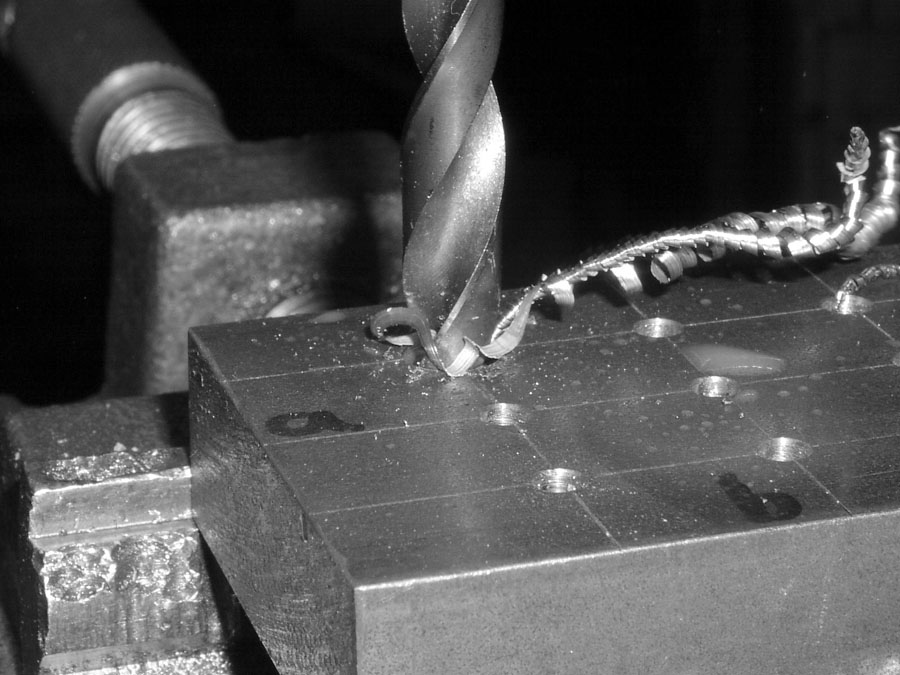
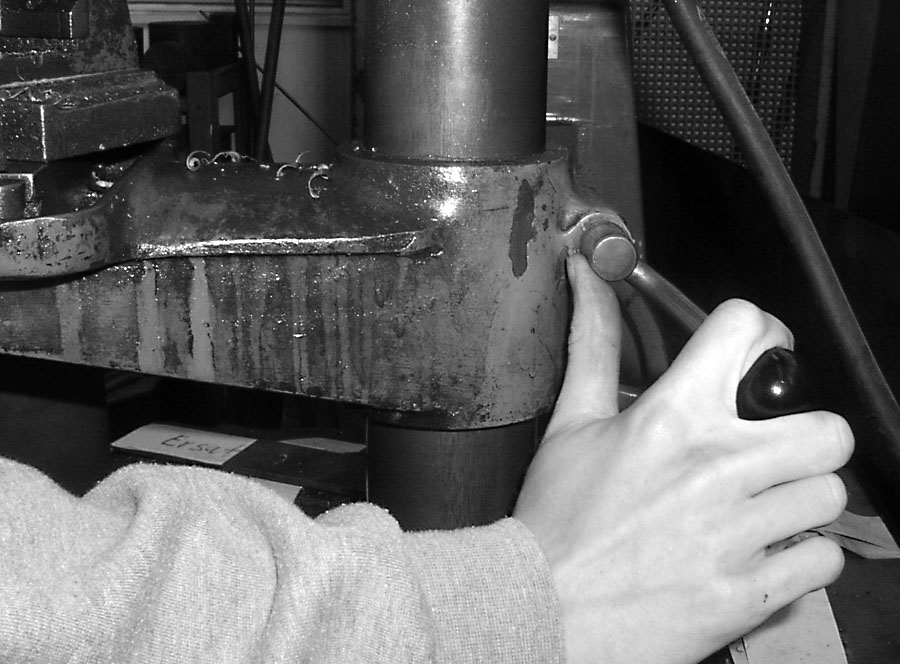
Bohren-Praxis
Ist die ganze Theorie verdaut, sollte die Praxis mehr als leicht fallen: Bohrer ins Futter oder in die Spindel stecken, Drehzahl einstellen und losgebrettert. Sind Bohrer und Werkstück reichlich mit Bohrwasser geflutet, macht das Bohren ein schmatzendes und zischendes Geräusch.
Dabei wickeln sich die Späne wunderbar gleichmäßig zu beiden Seiten ab und werden möglicherweise so lang, dass man den Vorschub kurz unterbrechen sollte, damit sie abreißen. Mit der Handbohrmaschine ist das genau dasselbe: Bohrung anpeilen, vorsichtig anbohren und los.
Eine ganz böse Tretmine ist, das auslaufende Schnellwechselfutter der Säulenbohrmaschine mit der Hand abzubremsen, um den Bohrerwechsel eine halbe Sekunde schneller zu machen: hängt hier ein Span, ist die Handfläche Fleischsalat.
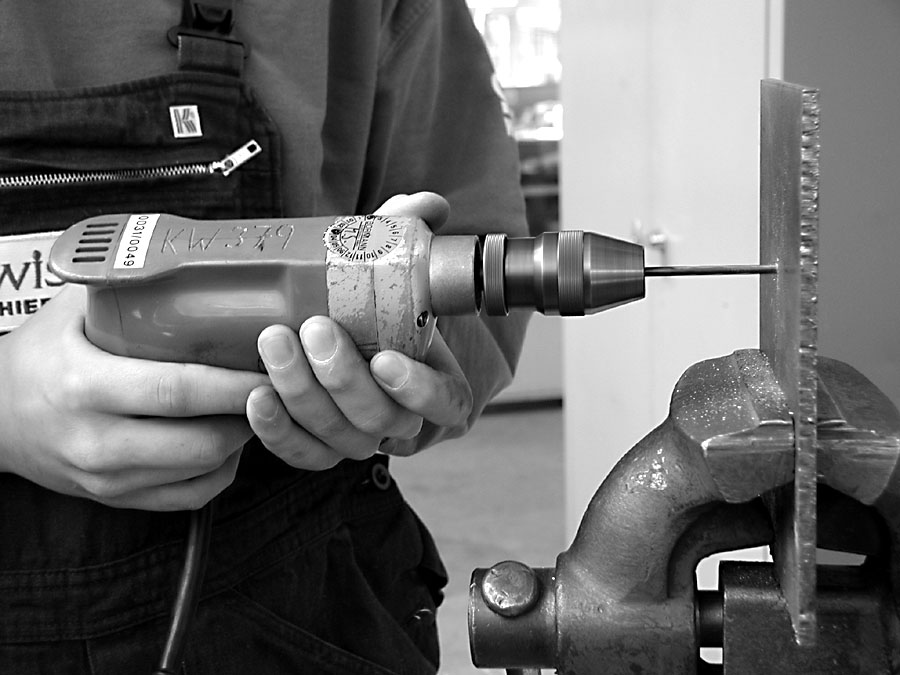
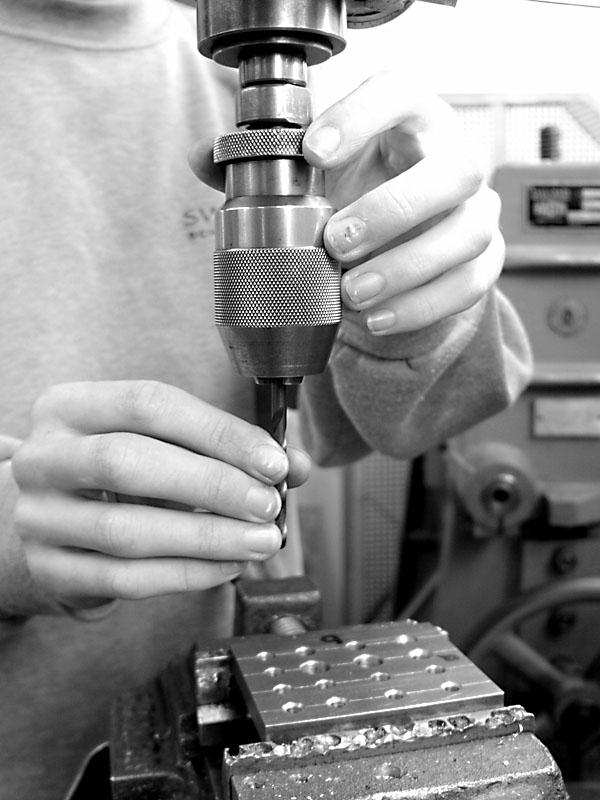
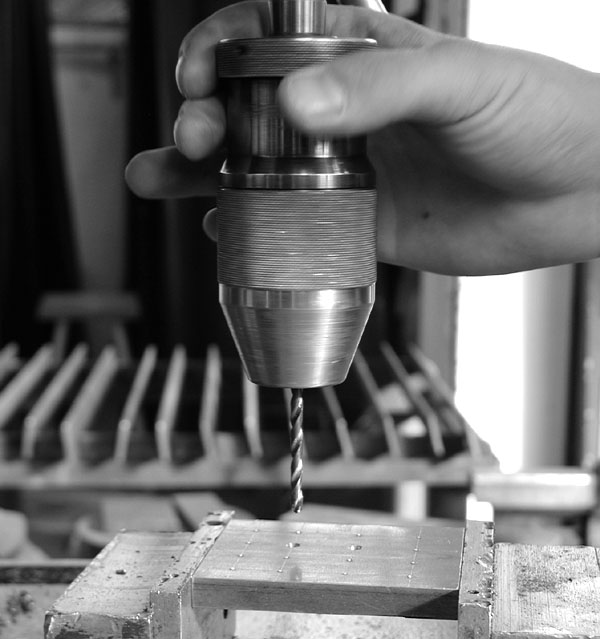
Aluminium zerspanen
Die beschriebenen Schnittgeschwindigkeiten beziehen sich auf Stahl, genauer: schnöden Baustahl. Alle härteren Materialien sollte man langsamer angehen und möglicherweise auf die niedrigste Drehzahl runterschalten, damit das Bohrwerkzeug nicht in Rauch aufgeht.
Bei allen anderen Materialien wie z.B. Aluminium- oder Magnesiumlegierungen ist noch dazu eigentlich ein anderer Bohrer nötig. Das Zeug hat nämlich die unangenehme Eigenschaft, zu schmieren und verklebt die Spannuten.
Soll viel Alu zerspant werden, lohnt sich die Anschaffung eines Bohrers für weiche Materialien. Das Kühlmittel ist in diesem Fall auch kein normales Bohrwasser, sondern Petroleum. Bronze oder Messing lassen sich natürlich auch zerspanen, verhalten sich aber wieder anders: dieses Zeug produziert extrem kurze Späne ist richtig rationell nur mit anders geschliffenen Werkzeugen zu bearbeiten.
Generell gilt aber, dass beim Bohren alles erlaubt ist, was zu einem guten Ergebnis führt. Und wie schon eingangs erwähnt, macht es durchaus Sinn, ein Stück Alteisen aus der Schrottkiste zu kramen und mit verschiedenen Durchmessern zu zersieben. Dabei lässt sich nicht nur mit Schnittgeschwindigkeiten und Drehzahlen herumspielen, sondern auch das Schleifen von Spiralbohrern üben.
Vor allem bekommt man dabei Gefühl für Vorschub, Drehzahl und das Geräusch, mit dem sich Stahl in Span auflöst. Noch mehr Gefühl braucht man, um die so entstandenen Bohrungen zu entgraten, zu senken oder aufzureiben. Wie das genau geht, zeigt die nächste Folge der ja scheinbar nie endenden Reihe auf Autoschrauber.de.
Span um Span
Wichtiges Utensil neben Bohrmaschine, Bohrer und Werkstück ist die Schutzbrille. Auch wenn der Kollege lacht und einen als Made zeiht: der gute Mann hatte noch keinen Span im Auge. Diese Späne sind überhaupt ein wirkliches Übel und mitunter so rasiermesserscharf, dass man sich damit bis auf den blanken Knochen schneiden kann.
Weil eine Säulenbohrmaschine zudem oft mehr als 1 kW an die Welle bringt, steht das auch beim Bohrer an und lässt Werkstück, Schraubstock und den ganzen Mann munter rotieren, wenn sich der Bohrer verhakt.
Als goldene Regel gilt deshalb, Werkstücke ordentlich festzuspannen, sobald der Bohrerdurchmesser 10mm überschreitet. Für diesen Zweck verfügen die Tische von Säulenbohrmaschinen Nuten, in die Nutensteine greifen und Schraubstock oder Werkstücke festklemmen.


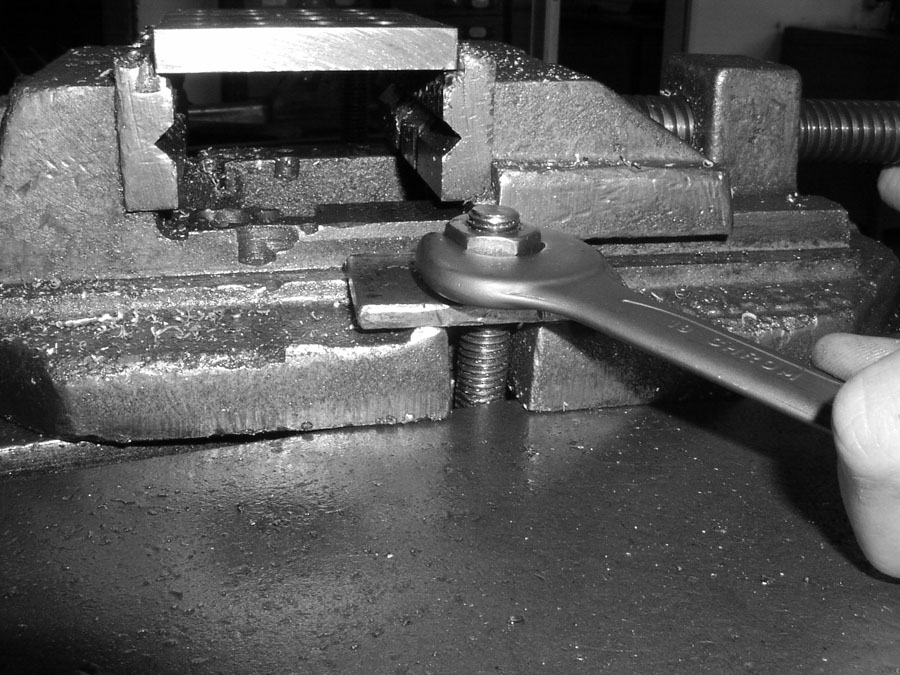